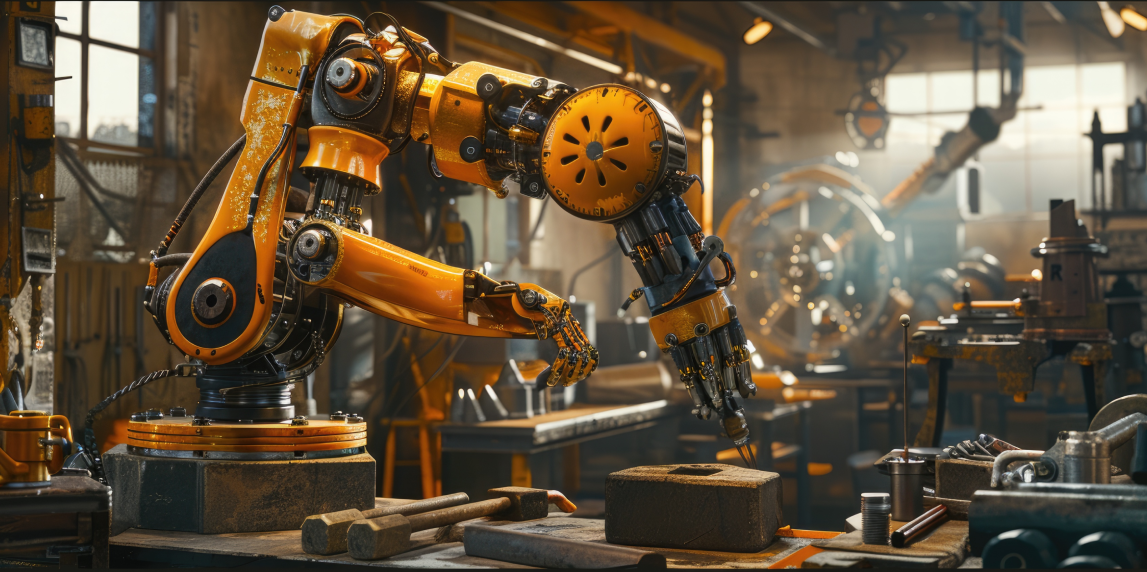
The foundry industry has traditionally been labor-intensive, involving manual processes that can be hazardous and time-consuming. However, the integration of robotics into foundry operations is transforming how casting and material transport are conducted, enhancing efficiency, safety, and overall productivity. This article discusses the various ways robotics is redefining foundry operations.
Robotics in Casting Processes
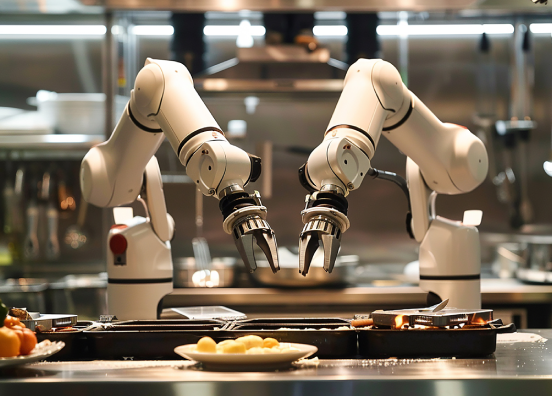
Robots are increasingly being utilized in various stages of the casting process, such as mold preparation, pouring molten metal, and handling finished products. For instance, robotic arms equipped with specialized tools can handle the precise movements required for pouring molten metal into molds, minimizing human exposure to high temperatures and hazardous materials.
Foundry Robotics Efficiency
Real-Time Casting

Enhancing Material Transport
Material transport is another critical area in foundry operations that benefits from robotics. The handling of heavy and hot metal components poses significant risks to workers. By integrating autonomous guided vehicles (AGVs) and robotic transport systems, foundries can streamline the movement of materials from one stage to another.
Companies like KUKA and ABB have developed robotic transport solutions that can operate in extreme conditions, including high temperatures and heavy loads Leistertech Projects
These systems not only improve safety by reducing manual handling but also optimize workflows by ensuring materials are delivered where and when needed, thus minimizing downtime.
Quality Control and Inspection

In addition to handling casting and transport, robotics also plays a crucial role in quality control. Automated inspection systems equipped with advanced imaging and sensor technologies can assess the quality of cast products without manual intervention. This automation allows for continuous monitoring, ensuring that defects are detected early in the process.
Robotic inspection systems can quickly analyze products for dimensional accuracy, surface imperfections, and other quality metrics. For example, Creaform’s robotic inspection solutions offer non-destructive testing methods that are faster and more accurate than traditional manual inspections Leistertech Projects
Safety Enhancements
Boosting Safety in Foundries
Enhancing Safety in Robotics
Future Trends in Robotics for Foundries
As technology continues to evolve, the future of robotics in foundries looks promising. Innovations in artificial intelligence (AI) and machine learning are paving the way for more sophisticated robotic systems that can adapt to changing conditions and learn from their environment. This adaptability will enhance the efficiency and flexibility of foundry operations.
For instance, the incorporation of AI-driven predictive maintenance solutions can ensure that robots and machinery are serviced proactively, reducing downtime and enhancing overall productivity. Moreover, advancements in collaborative robots (cobots) allow for safer interactions between human workers and robotic systems, further enhancing operational efficiency .
The integration of robotics into foundry operations is redefining how casting and material transport are conducted. From improving safety and efficiency to enhancing quality control, robotic systems are revolutionizing traditional practices within the industry. As technology advances, the potential for robotics to further transform foundry operations will only increase, paving the way for a more efficient and safe manufacturing environment.
- FANUC Robotics
- KUKA Robotics
- ABB Robotics
- Creaform
- RobotIQ – The Future of Robotics in Manufacturing

lpipl
lpiplYou Might Also Like
- lpipl
- 0 Comments
- lpipl
- 0 Comments
- lpipl
- 0 Comments