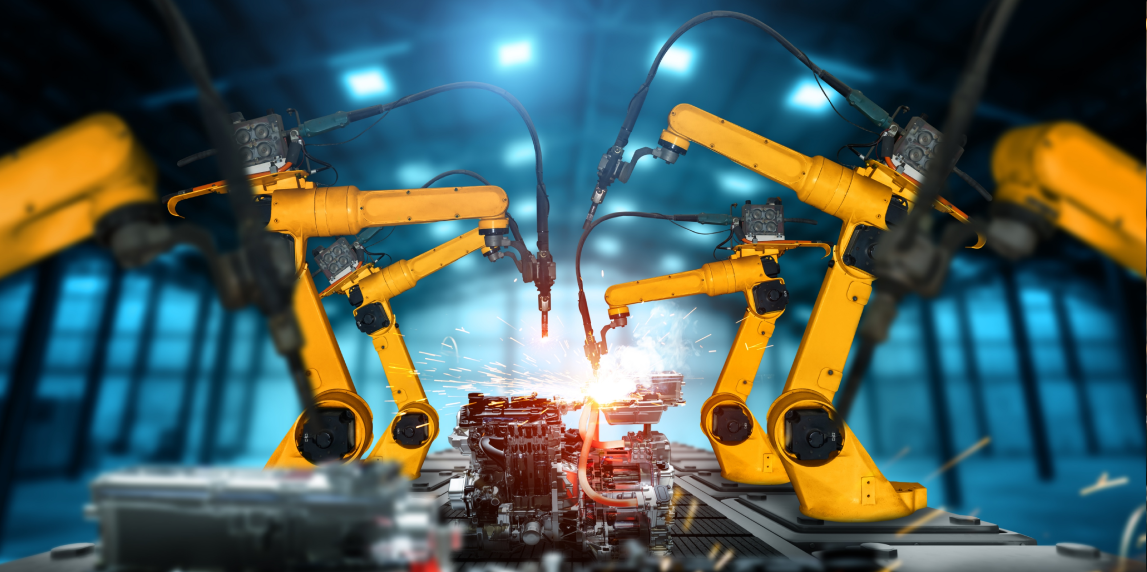
Automation is reshaping the landscape of heavy industries, particularly steel production and foundries. These traditionally labor-intensive sectors are now leveraging cutting-edge technologies to enhance efficiency, precision, and safety while reducing costs and environmental impact. This transformation is setting new benchmarks for productivity and competitiveness.
How Automation is Revolutionizing Steel Production
Steel production is a complex process involving multiple stages, from raw material handling to smelting, refining, and shaping. Automation is bringing about significant improvements at every stage:
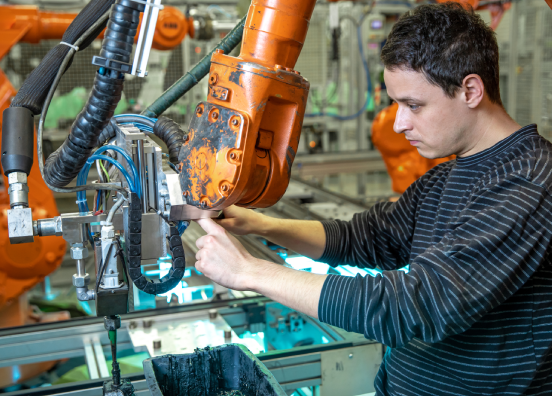
Enhanced Efficiency
Automated systems streamline operations, reducing production time and labor costs. Advanced machinery, like robotic arms and automated conveyors, ensures smooth material flow and minimizes bottlenecks. For example, automated hot billet shearing machines process steel at high speeds with minimal downtime, significantly boosting throughput.
Improved Precision and Quality
Energy Optimization
Advancing Safety Standards in Foundries
Foundries, which handle molten metals and heavy machinery, are among the most hazardous workplaces. Automation has transformed these environments by introducing technologies that minimize human exposure to risks:
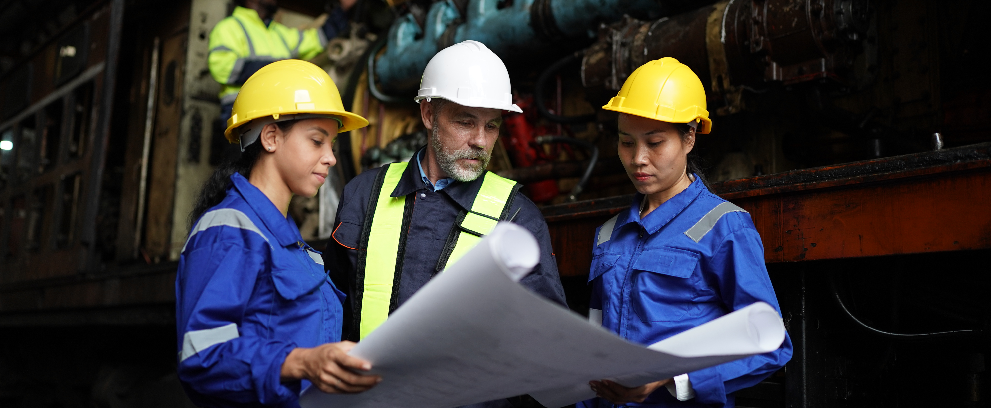
1. Robotic Material Handling
Automated systems handle heavy and hot materials, such as molten metal and castings, reducing risks of burns and injuries. Tools like robotic grab buckets and lifting magnets ensure precise and safe material transfer.
2. Improved Workplace Ergonomics
Automation relieves workers from repetitive and physically demanding tasks, reducing strain-related injuries. Hydraulic pushers and automated pouring systems streamline operations, allowing workers to focus on supervision rather than manual labor.
3. Real-Time Monitoring for Safety
Automation integrates sensors and real-time monitoring systems that detect anomalies, such as overheating or equipment malfunctions. Predictive maintenance enabled by these systems prevents accidents and costly downtime.
The Role of Data and Smart Technologies
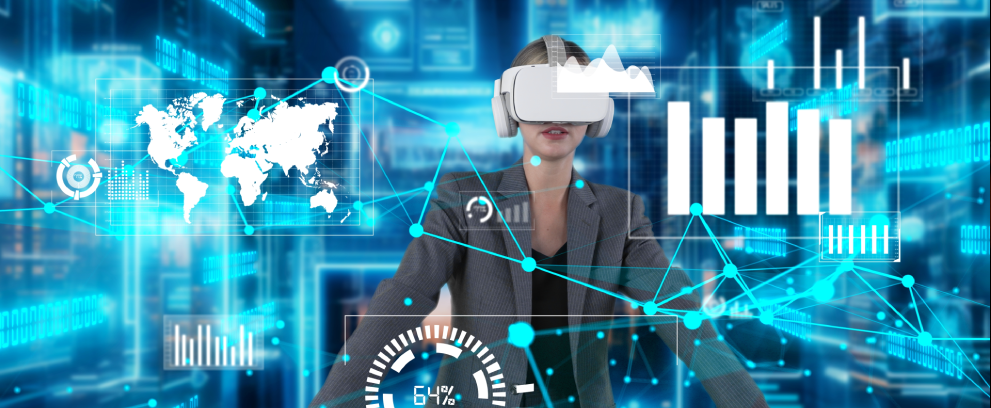
Real-Time Monitoring and Optimization
Sensors embedded in automated machinery provide real-time data on temperature, pressure, and equipment performance. This data is analyzed to optimize operations, reduce waste, and improve production efficiency.
Predictive Maintenance
Automation systems predict equipment failures before they occur, reducing unplanned downtime. For instance, smart vibration monitors on machines like lining vibrators detect wear and tear early, ensuring timely interventions.
AI-Driven Decision Making
Artificial intelligence (AI) algorithms analyze production data to suggest process improvements, optimize workflows, and forecast demand.
Learn how AI is transforming manufacturing from McKinsey & Company.
Benefits of Automation in Heavy Industries
Increased Productivity
Cost Saving
Environmental Sustainability
The integration of robotics into foundry operations is redefining how casting and material transport are conducted. From improving safety and efficiency to enhancing quality control, robotic systems are revolutionizing traditional practices within the industry. As technology advances, the potential for robotics to further transform foundry operations will only increase, paving the way for a more efficient and safe manufacturing environment.
LeisterTech exemplifies the impact of automation in heavy industries. Their advanced machinery, such as hot billet shearing machines, hydraulic pushers, and lifting magnets, integrates automation to enhance efficiency and safety. By adopting LeisterTech’s solutions, manufacturers can stay ahead in this competitive landscape.
Automation is not just a trend; it’s a necessity for the evolution of steel production and foundries. As industries continue to adopt these transformative technologies, they are paving the way for a smarter, safer, and more sustainable future.

lpipl
lpiplYou Might Also Like
- lpipl
- 0 Comments
- lpipl
- 0 Comments
- lpipl
- 0 Comments